

“REVO gives us a clear competitive advantage I have no doubt it will help us win work”, says Alan Naylor, ANT’s technical director. Some parts need 100% inspection, while others must have at least 1 in 10 inspected. CMM inspection of finished parts is taken for granted in the aerospace industry, and ANT has to offer it to their customers as part of the manufacturing process. “The closest alternative was a system costing five times as much, but it wouldn’t have achieved the same levels of throughput.”ĪNT produces over 1000 different machined parts, approximately 85% of which are supplied to the aerospace industry, requiring a high proportion of final part inspection. “Now that we have the new machine we are playing a different game – there is no other option to REVO, nothing else comes close”, adds Shaun Rowley. However, following the purchase of a new coordinate measuring machine (CMM) equipped with a Renishaw REVO five-axis scanning system, the situation has changed markedly.

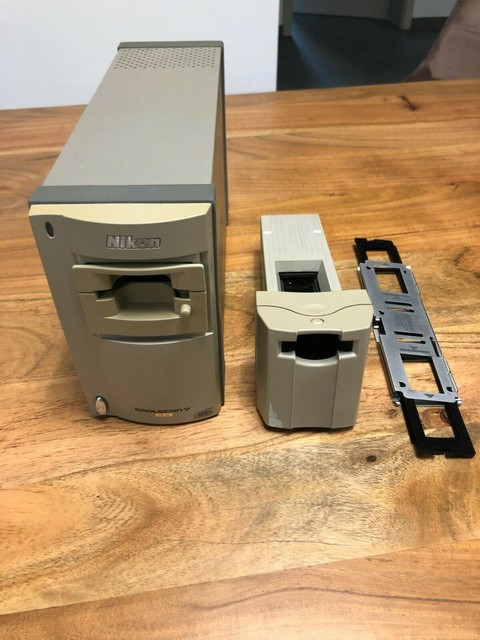
These are expensive parts without any value being added”, says Shaun Rowley, ANT’s manufacturing and sales director. “There were thousands of non-productive hours a year where parts were either in inspection or waiting to be inspected. When aerospace sub-contractor ANT Industries carried out a study on its production processes with the aim to make improvements, it was clear that inspection was a major bottleneck.
